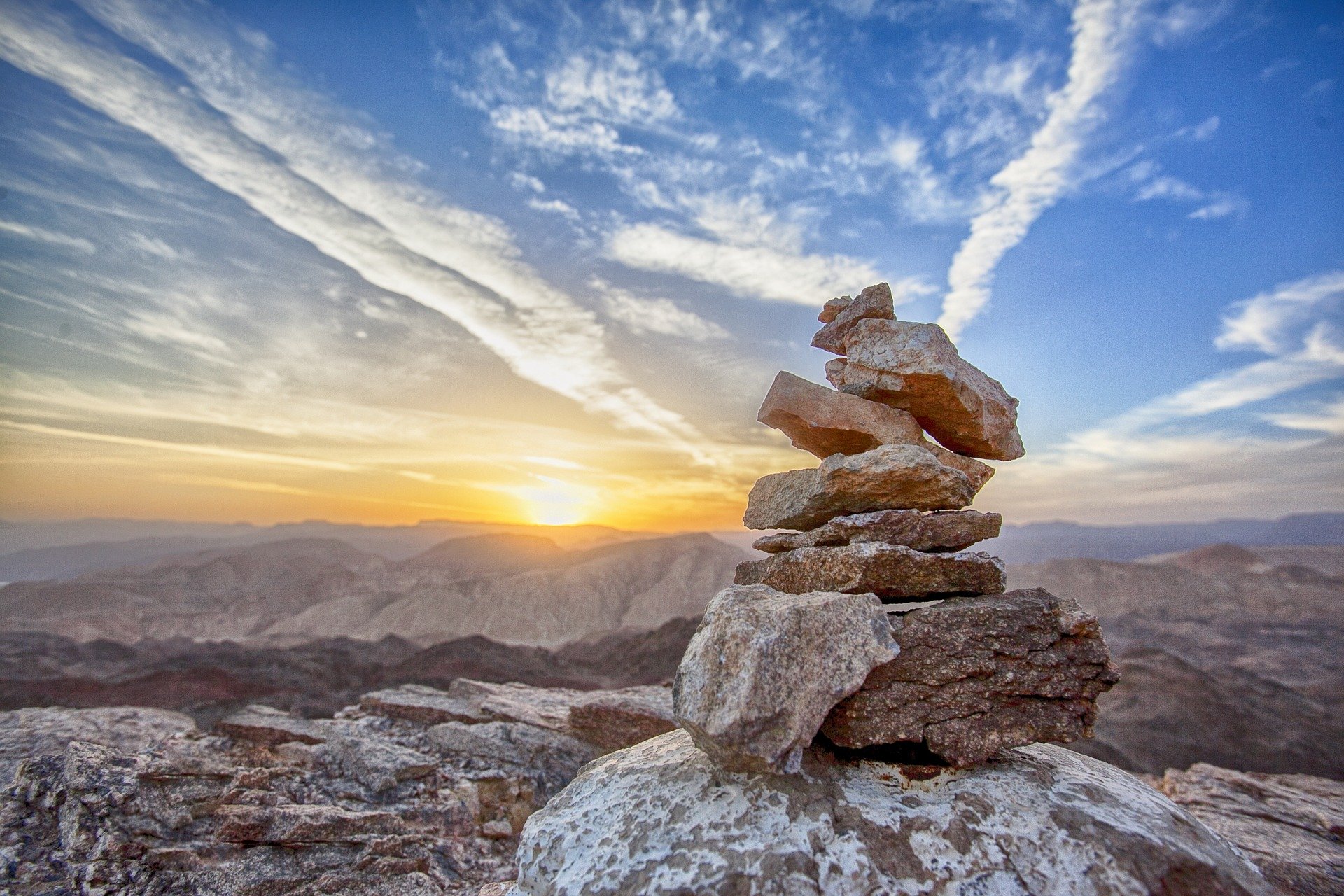
Lean Management is known for reducing waste, but it also encompasses the 3M approach, that is waste (muda), variability (mura), and overutilization (muri).
Last week, we started a new series on Lean Management and the importance of humans in this philosophy. In that article, I was mentioning that several articles have given Lean a bad reputation in the way that lean organizations were able to face the highly volatile market demands during the pandemic. It is true that the just-in-time (JIT) approach was challenged with the uncertainty, complexity, and ambiguity that the last year brought upon all of us. But Lean management is a lot more than JIT, it’s more than cost reduction. Lean Management is a balanced approach, and we will address its different facets in this week’s article.
Be sure to read the entire series by subscribing to our newsletter.
Balanced Approach
More often than not, Lean is equal to waste reduction which drives cost reduction. It is an important facet of Lean management. Who decides what is waste? The customer. He/she is the reason why we do what we do and offering them what they want is at the core of the Lean philosophy. For that we need to know what they want and when they want it. And anything that doesn’t help us reach that can be considered a waste. But what is waste? It can be present in various forms, such as transport, inventory, waiting, motion, overproduction, defaults, over-processing, and skills, and represents any misuse or ineffective process steps. According to Ohno, the father of the Toyota Production System, waste is “the needless, repetitious movement that must be eliminated immediately.” (Ohno, 1988, p. 57) One key question is whether any presence of these is automatically considered a waste. And to get to the answer, we need to consider value-added (VA) versus non-value added (NVA) activities. VA activities are steps that transform the material, for example when the raw material becomes a finished product, that changes the shape or the character of the product (1). While a NVA activity is not directly linked to that transformation process. It can be moving parts into a production area (transport), the operator having to move from one station to another station to bring the necessary tools closer (motion), a large, stocked quantity that is not used (inventory). In the service industry, VA can be transforming data into readable and actionable information that the customer can use and NVA can be the administrative process of opening up a new client account.
The second ingredient of the balanced approach is about understanding the variability or unevenness of demand and our operations. This variability can come from customers’ demands, from customer service requests, and from wanting to hit a certain number at the end of the month or quarter. We then increase our production to match those requests. And this leads straight into the third ingredient.
The third ingredient is the overutilization of our resources, human and equipment. In the first article, I talked about trusting and respecting our employees and their knowledge about what they do. This week, I address how we use their skills and work hours. This ingredient refers to an overburden or an unreasonable process that pushes people and equipment to work beyond the limit of what is realistic. Why is this such a potent ingredient? Because it’s been assessed that beyond a certain number of hours per week, employees stop being productive and the risk of errors, accidents, and sickness(2) as well as the risk of creating defects in production(3) increase. In terms of equipment, the unreasonable utilization can lead to unnecessary strain on the mechanics and the parts, preventive maintenance not being executed, and added defects generated. All this can potentially damage the equipment because of the level of use beyond what it was conceived for. The effects of this unreasonable utilization, on both humans and equipment, can then lead to generating wastes in the processes.
But if waste is so important, why don’t we just remove it all from our processes? The answer is: it’s not that easy! And that is where we need to consider this balanced approached. It’s actually like pizza and yes, the pun is again intended. Pizza has dough, sauce and toppings. Each of these can be something on their own. But it’s when they are put together and in the right amounts that they become a great pizza. Those amounts can differ from person to person. For example, I may like a lot more cheese than someone else. But it’s still a pizza. For Lean Management to be effective, we need to consider what is the right mix to reduce waste, unevenness, and overburden. The reality is that none of these can be completely removed, they depend on your network of partners, your suppliers, the carriers, as well as your customers. For example, if I carry a higher level of inventory for part A than for part B, am I generating waste? Maybe or maybe not. If the supplier of part A is farther away, can only provide a certain amount at a time, and I use part A to manufacture 3 different high-selling products it might make sense to have more inventory than for part B, whose supplier is down the street, has no limit on quantity and I only use that part on one product that I barely sell.
Understanding what happens in our supply chain is critical to determining the right balanced approach: what our customers want and when so that we can then determine what is the waste that we can address to reduce unevenness and overburden. Next week, let’s look at Lean’s spicy toppings. To receive all the articles, subscribe to our newsletter.
“The inevitable result is that unevenness creates overburden that undercuts previous efforts to eliminate waste” Jim Womack.(4)
CONTACT US TO FIND OUT MORE!
Photo Credit: Gidon Pico de Pixabay
(1) Ohno, T. (1998) Toyota Production System: Beyond Large-Scale Production. New York: CRC Press.
(2) Pencavel, J. (2013) The Productivity of Working Hours. Standford University. https://siepr.stanford.edu/research/publications/productivity-working-hours
(3) Liker, J. K. (2004) The Toyota Way. New York: McGraw-Hill.
(4) Womack, J. (2006) Mura, Muri, Muda? Lean Enterprise Institute. https://www.lean.org/womack/DisplayObject.cfm?o=743