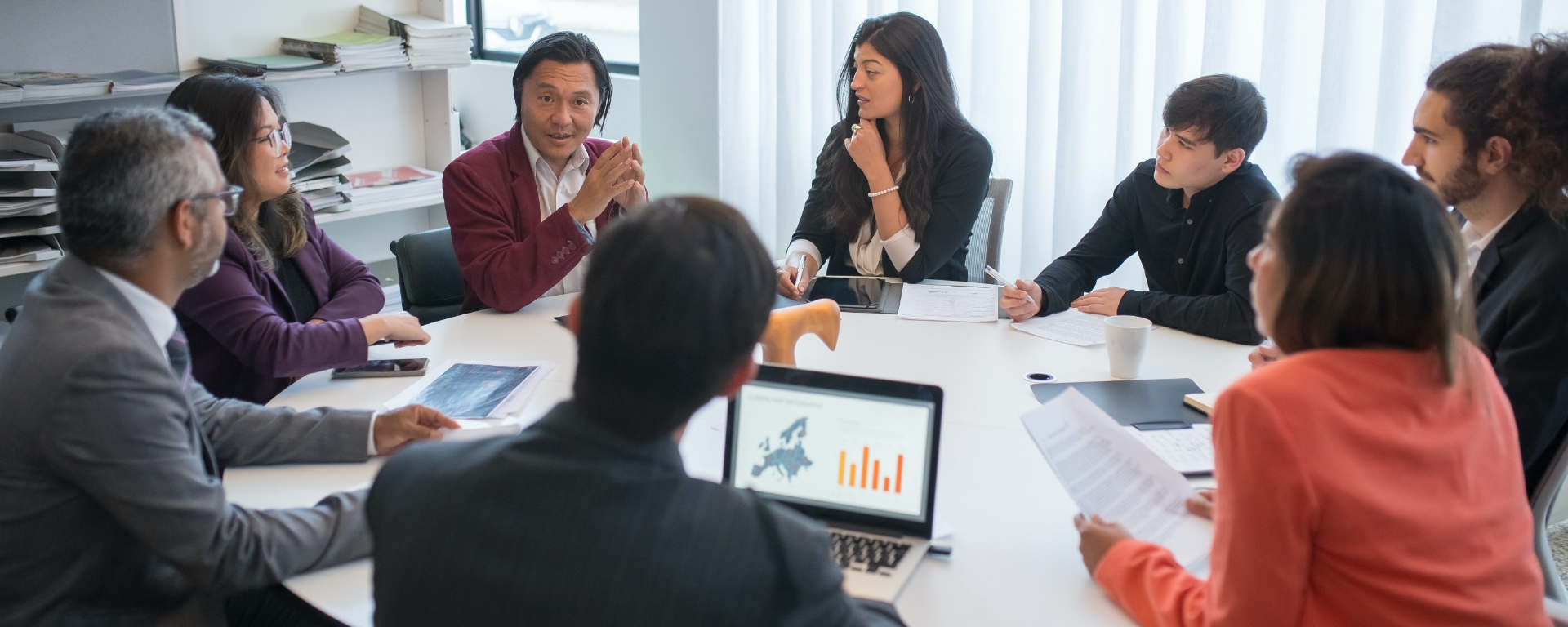
Lean Management
The benefits of Lean Six Sigma
Contrary to Lean manufacturing, Lean management applies not only to production, but to a company’s overall structure. We work with your leadership and all your teams to design, implement and communicate strategies and policies that will have a long-term impact on the quality of your products and services.
In addition, Lean management and the agile Six Sigma methodology are continuous improvement methods that have proven their worth in many industries and sectors of activity. Unlike Lean manufacturing, these methodologies are suitable for service companies, businesses and public bodies such as municipalities.
Lean Six Sigma, for its part, is the combination of these methods and is recognized as the fusion of continuous improvement and operational performance best practices, no matter the industry. That’s why, at Aristeío, we are Lean Six Sigma experts and use it as our primary work methodology.
We operate according to an established work sequence that captures the information we need to identify the right performance indicators and make the right decisions.
Our methodology focuses on the productivity, quality and cost management aspects of performance. Its role is mainly to reduce waste and eliminate defects or variations in companies’ production processes. For us, the Lean Six Sigma approach is much more than a series of tools: it is a corporate culture where we all aim together to achieve excellence every day.
Aristeío supports you from beginning to end as you roll out and start using Lean Six Sigma. Contact us to implement quality improvement tools or to provide executive coaching to decision makers and management teams.
Increase your teams’ skills and build commitment
We train your teams to learn how to identify problems themselves, work together to find causes, and co-develop solutions. This sharpens everyone’s skills and increases teams’ agility and resilience, which, in turn, contributes to developing successful and sustainable solutions.
Improve customer and stakeholder satisfaction
We perform an in-depth analysis of customer experience (CX) to capitalize on what really matters to your customers. This analysis highlights what customers consider as adding value and how you could better serve them.
Reduce waste
Once customers’ expectations have been identified, we define superfluous steps and tasks that do not add value for customers. Focusing on the right things helps you save resources and maximize your earnings.
Increase productivity
We help you consolidate the previous steps to manage your teams efficiently, eliminate overproduction, properly manage your inventory and logistics and control your deadlines—all of which lead to the next step.
Standardize processes, products and services
We support you in standardizing processes so you can deliver the same quality every time and keep your customers satisfied. This helps us both create a common knowledge pool and work together to improve your performance.
Efficient management of time and priorities
By coordinating your operations and regulating your workflow, you will not only save physical resources, but also valuable time. You will be able to always deliver the right products, at the right time, in the right quantity and in good quality.
Reduce production costs
After performing a comprehensive organizational diagnostic that includes all the previous steps and implementing the targeted improvements, you will see a reduction in production costs that you will be able to sustain.
Lean manufacturing
The 5S of Lean
We also support heavy industries, municipalities and manufacturing companies in planning and designing production and warehouse spaces.