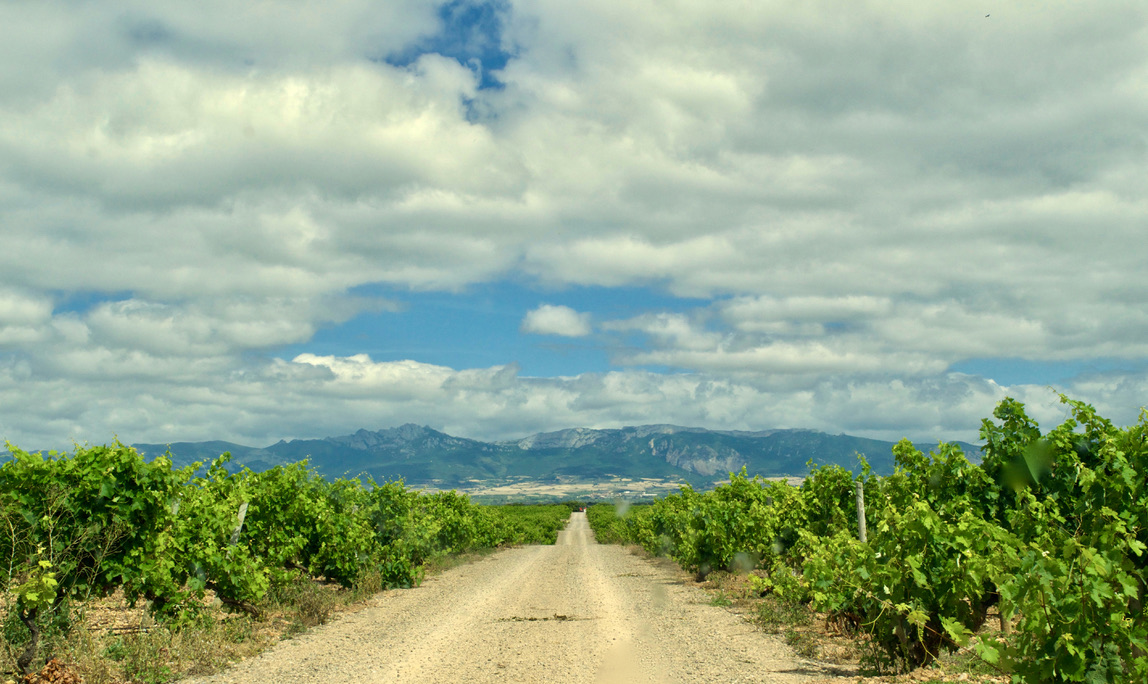
Lean Strategy is part of the Lean Management principles and culture to ensure that everyone is working towards achieving the same goals!
A few weeks ago, we started a new series on Lean Management. We talked about the importance of humans as well as the balanced approach in this philosophy. What I’ve come to realize over the years, is that Lean management is a lot more than the tools. It may have its roots in manufacturing, but Lean Management applies to all kinds of industries and is a based on a forward-looking vision that encompasses the entire organization to achieve excellence and continuously work to better serve the customers.
In this week’s article, we will discuss a few approaches that help look into the future and build string ties within the organization. Make sure to read the entire series.
Lean Strategy
For any organization, having a clear vision of where it wants to go is crucial to reaching the objectives and the values are what shows everyone how to work towards those objectives. In Lean, the vision is called the True North, which represents “The ideal way in which things should be done” (1). But how can we achieve this vision? Lean Management offers a few ways.
Strategic Choices
First, a strategic planning process that starts at the highest level of the organization where aggressive and ambitious goals are set. These then get cascaded down to the different levels where each team reviews them and identifies ways in which they can contribute to reaching these objectives and how they will measure their efforts and results. The data then gets returned to the top management, for another review, and so on. This communication iterative process ensures viable and continuous dialogue between all the levels of the organization. Furthermore, it ensures that all employees are aware and understand the vision and the goals that the organization is working towards as well as how they contribute to the results.
Performance Management Deployed by Lean Strategy
Second, a dedicated place or room where all the performance measures are tracked and can be viewed by all in a comprehensive overview. This room, often called a control room or a war room, showcases the performance measures that were determined during the strategic planning exercises. Here we can see the True North that the organization is working towards as well as the different performance measures that ensure that everyone is working in the right direction and according to the shared vision.
But this is not just a room where numbers and graphs are posted on the wall or TV. It is a place that is intrinsically connected to the management system and where leaders gather to discuss and address the goals and the results. Using colour coded information, it is easy to see the goals that are achieved (in green), the ones that are struggling (in yellow), and the ones not meet (in red). This simple method allows the meetings to be effective because the energy and effort can be placed on where it is needed, the reds and the yellows. The greens will serve to celebrate the wins and encourage team members to continue with what they are doing. All this information also helps to gather the managers in addressing situations that could not be solved at operational levels and to establish continuous improvement cycles to realign the results towards the goals.
Daily Management System to Ensure Strategic Focus
Third, a management system that shares information daily on safety, planning, productivity, quality, and costs by having this information available to all wherever the work is conducted on visual stations. Again, this openness ensures that all team members have an understanding of the overall objectives as well as their personal contribution to the success. These stations are also the location where daily meetings are conducted between the supervisor and the employees. They review the elements that pertain to their activity, address the challenges that they are going through, the continuous improvement projects that they are working on, and any other relevant information that is part of their agenda. These meetings also help identify what processes are struggling and the issues that cannot be solved at that specific level. The supervisor then meets with his/her superior and provides information on the elements discussed with his/her team that need to be raised to their level, and so on. These bottom-up pieces of information get pushed up along the chain of leadership and new data gets pushed top-down to reach them again. It ensures that each level is working on solving the issues they have some control over and that whatever needs to be pushed up is done so in a timely manner.
These three interconnected management processes ensure that the organization works as a whole to reach the same objectives, that the information is shared rapidly and efficiently throughout the organization, that issues get solved, and that work continues to be done to better serve the customer.
Personal note
I’m certain that you will have noticed that I have not included any Japanese terms in any of my articles about Lean. I’ve learned Lean through work experience, studying, and coaching and am familiar with the Japanese terms. But I have purposely stopped using them when talking to people for a few reasons.
- I find that when I speak with them, it creates alienation between the ideas I’m trying to convey and what my interlocutors are paying attention to.
- My Japanese is not great, well let’s be honest, it’s non-existent! So, I don’t know if my pronunciations are correct or not, and I would not want to offend people with mistakes in how I say the terms.
- Most of the people that I talk to do not speak or understand Japanese and the terms get lost in translation.
I’d rather speak in a plain manner that most people can understand because the message of what Lean Management can do for organizations and their people is too important to lose with words that we don’t fully understand.
To receive all the articles, subscribe to our newsletter.
CONTACT US TO FIND OUT MORE!
_________________________________
About Veronica B. Marquez
I help growing manufacturing and service organizations scale without chaos—by turning operational challenges into sustainable performance gains. My superpower is making strategy real at every level of the business: connecting people, processes, and purpose to drive productivity, engagement, and resilience. I bring clarity to complexity and help teams execute better, faster, together. Through a proven lens of operational excellence, continuous improvement, and supply chain optimization, I work with leaders to align efforts, simplify execution, and create systems that actually support growth.
Named one of the Top 50 Experts in Operational Excellence by the PEX Network, I bring over 20 years of experience across sectors like manufacturing, distribution, mining, and public services. I teach Lean Six Sigma at the executive education level, lecture on service design in a master’s program, and host a LinkedIn Live series focused on Excellence in Industry 5.0. Ready to explore how operational excellence can transform your business? Reach out https://www.linkedin.com/in/veronicabm/.
Photo Credit: VB Marquez
SOURCES
(1) Landry, S. & M. Beaulieu (2021) Lean, kata et système de gestion : réflexions, observations et récits d’organisation. 2e éd. Montréal : Les Éditions JFD inc.
(2) Liker, J. K. (2004) The Toyota Way. New York : McGraw-Hill.
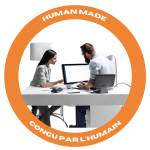
Human made