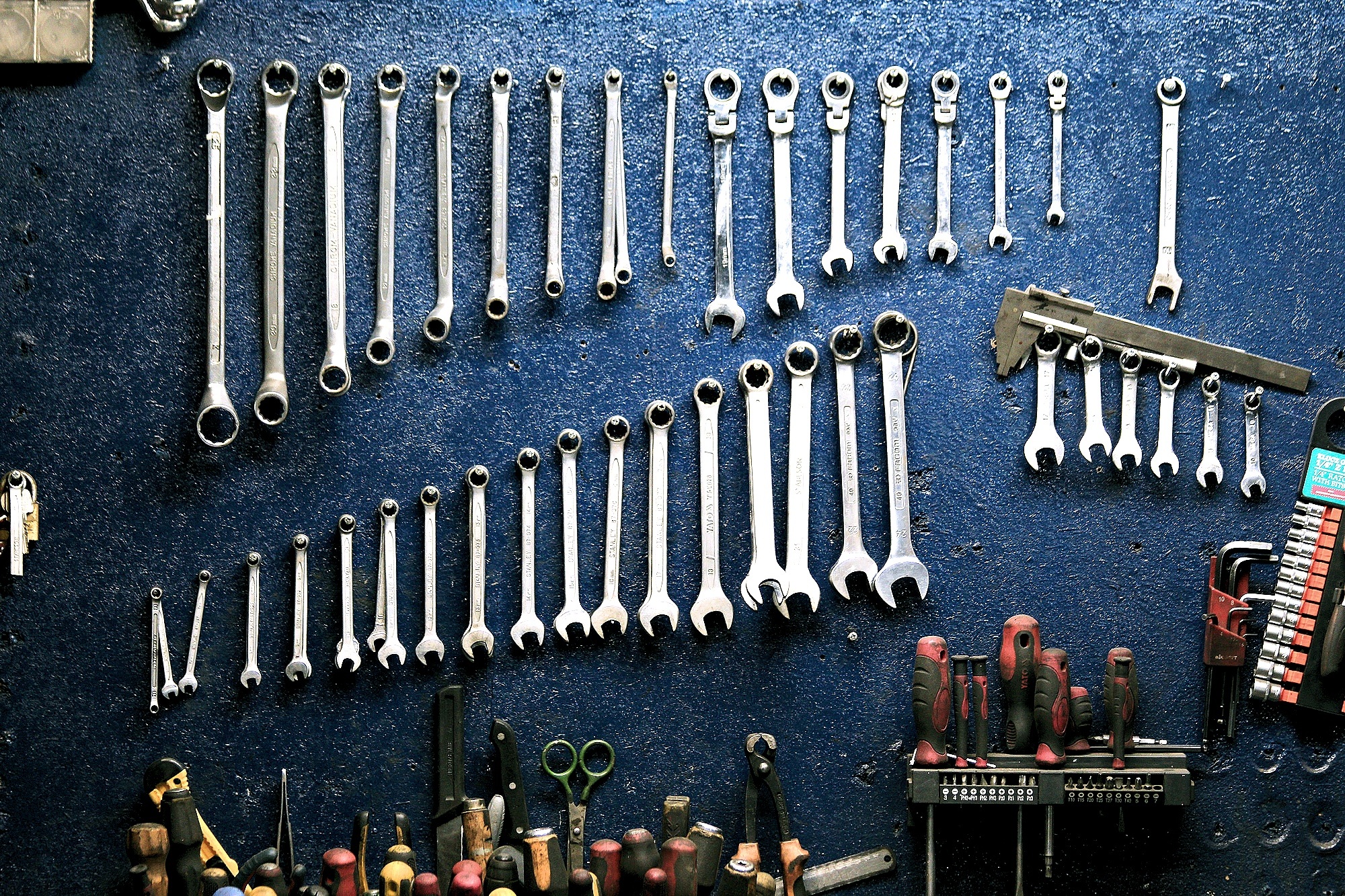
Have you ever looked for something and then realized how much time you wasted not finding it? How frustrating! You could have done so much more with that time if you had implemented a 5S organization!
Imagine if an employee in a workshop could not find his or her tool, what a loss of efficiency! Or if an employee gets injured because of a wrong indication of a hazard, that’s a much longer loss of time and consequently a slowdown in the performance of his team. What about the feeling of the employees in these moments… The frustration, the discouragement that this can cause, or even a total disengagement of the employee.
We all wish we had workshops and warehouses as tidy as our grandfather’s shed, where every tool has its place, rather than our teenager’s bedroom, where everything is lying around on the floor and the risk of accidental snagging in the carpet is much greater!
The 5S Organization Method
About fifty years ago, Toyota understood this. They created the 5S method and implemented it in all their production lines. With constant improvement in mind, they developed a solution to increase performance on the shop floor while ensuring the safety of employees.
This visual management approach makes it easy to identify where things are. It allows you to:
- Improve
- productivity
- employee health, safety and wellbeing
- configuration and flows in the workspace
- Reduce
- wasted time
- purchasing costs of tools and equipment
- hygiene and sanitation problems
- Practice team discipline by setting and maintaining work standards.
What does 5S organization actually mean?
Well, each letter of the 5S represents a Japanese verb that defines an action. You will guess that these represent a category of actions to be worked on within a workspace, whether it’s a warehouse, a store, or even your garage!
Seiri: Select
First, we establish the sorting criteria. For example, let’s take the case of a maintenance workshop in a company. Can the tools be categorized? How often are they used? How many of these tools should I have? Are they really necessary?
Then it’s time to sort: which items are broken, non-functional? Should they be repaired? To give away? Keep them close to where the work is done? To keep, but further away? In this way, we can make an inventory of everything in the work environment and keep what’s needed to get the job done close to the workers.
Given that it’s quite possible that all the items have been taken out of storage, this is the ideal time to do a thorough clean-up! A fresh coat of paint can also help to create a clean, bright space!
Seiton: Situating
Since it’s quite possible that all the items have been taken out of storage, this is the ideal time to do a thorough cleaning! A fresh coat of paint can also help to create a clean, bright space!
Next, organize the space with shelving and storage systems. The aim of the storage equipment chosen will be to keep items in plain sight and in their place, so that you can easily see whether they’re there or not. We’ll also want to make sure that the visual management and identifiers used keep the space clean and uncluttered.
Finally, products are arranged according to frequency of use and size, to reduce unnecessary movement. At the same time, a list of stored items and their locations will help to ensure continuity of the organization.
Seiso: Shining
In order to maintain a clean space to ensure everyone’s safety and to help tidy up, a maintenance routine at the start and end of each shift is essential. Each employee is responsible for repositioning tools in their place and tidying up their workspace. In short, every employee will be able to start their day in a clean environment.
In addition, weekly audits carried out by employees and managers will make it easy to identify good work and quickly address possible improvements. Regular maintenance and prevention throughout the year will keep the workspace clean and safe.
Seiketsu: Standardizing
The fourth stage of the 5S organization, standardization, is supported by visual identification, which is very important in this stage, as it quickly indicates what needs to be done or avoided. Also, work instructions and warnings must be clear, simple to understand and standardized to maintain the first 3 steps. This is why we regularly use pictograms to show what to do and what not to do. The aim of this phase is to simplify the maintenance and sustainability of the work that has just been done!
Shitsuke: Sustain
The watchwords for this final stage: rigour and teamwork! Close monitoring with external and internal audits, as well as the implementation of written procedures, will allow validation of compliance with standards and their improvement. Finally, the visual management chart for the 5S organization will enable constant monitoring of the good work done and the improvements to be made. This new team routine for learning together how to maintain 5S is the start of continuous improvement! Employees learn to identify problems and work together to find solutions.
Support in Implementing the 5S Organization
When we support our customers in implementing this methodology, we encourage them to celebrate successes and highlight the efforts made by employees. With a shared commitment to success, it’s much easier to achieve objectives as quickly as possible. That’s why we also involve all the teams concerned in the implementation process and include them in our implementation strategy. This creates a real feeling among employees of participating in the advancement of a project for the good of the organization, better cohesion between the different groups, as well as simplifying their day-to-day work!
We offer training in the 5S organizational method, including an introduction to Lean and forms of waste. Don’t wait any longer and offer your team a safe and productive environment!
Schedule a meeting with us to find out how we can help you implement the 5S method.
Want to read more about continuous improvement? Check our blog