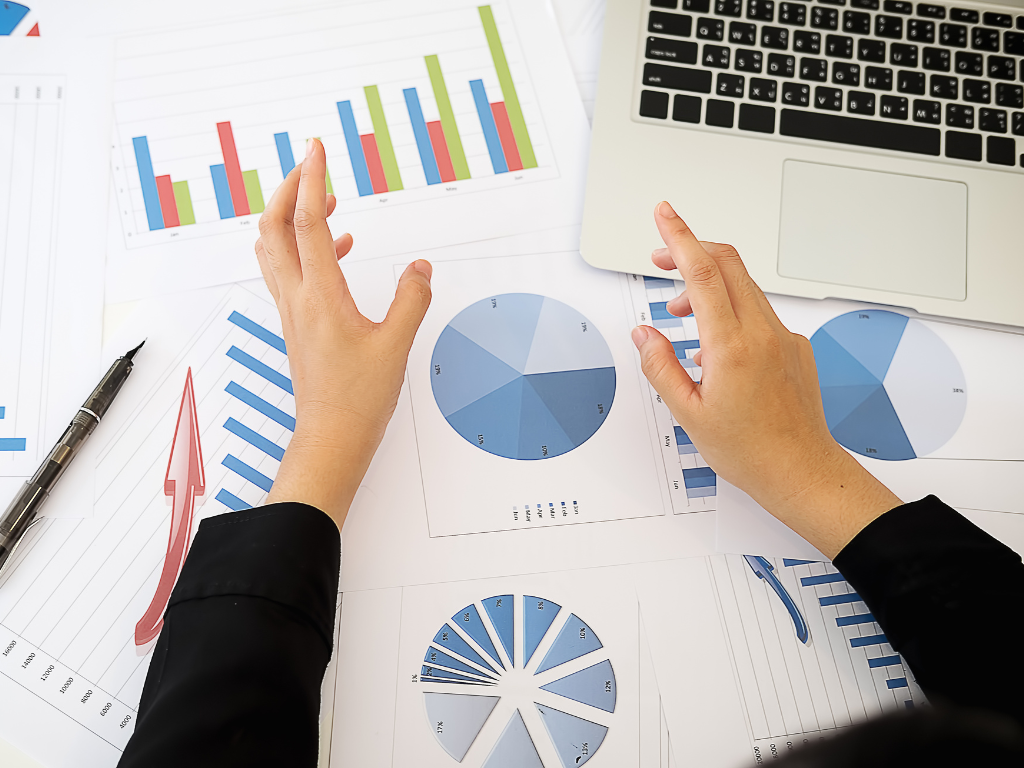
Growth ≠ Productivity: Why Continuous Improvement Is the Missing Link
Is your company growing—but things feel messier, not better?
If you’re seeing more errors, delays, turnover, or onboarding problems, you’re not alone. Many manufacturers between $10M and $20M in revenue face the same challenge: rapid growth without stable systems.
It’s tempting to jump straight to automation to fix the chaos. In fact, 62% of Canadian manufacturers are doing just that to improve productivity (CME Canada, 2024). But what if you started somewhere else?
Before you automate, invest in your people. The most resilient organizations use continuous improvement (CI) as the foundation for productivity—and a smarter path to automation.
What Is Continuous Improvement in Manufacturing?
Continuous improvement is a structured, people-first approach to making small, daily changes that improve processes. It helps teams work smarter—not harder.
CI is based on Lean and Kaizen principles, but it doesn’t require a massive program to start. You can begin with:
- Empowering employees to solve problems
- Making work visible and improvable
- Building daily feedback loops that support learning
💡 Learn more: Lean Management and People
Why CI Comes Before Automation
You can’t automate chaos. CI helps you build stability before scaling or digitizing.
Here’s what CI provides:
- A shared way of working
- Team ownership of processes and results
- Faster onboarding through visual, standardized work
✅ When your people know how to identify and fix problems, you reduce errors, downtime, and firefighting.
✅ One Aristeío client saw a 50% reduction in process steps and eliminated email-based communication for key tasks.
According to McKinsey, manufacturers using Lean and CI practices improve operational performance by 5–8% (McKinsey, 2022). That’s before automation even starts.
What Happens If You Skip CI?
Jumping straight to automation can backfire. Common issues include:
- High employee turnover
- Constant crisis management
- Inconsistent training and tribal knowledge
- Automation that doesn’t deliver ROI
62% of Canadian manufacturers are looking for higher productivity through the implementation of and adoption of technology (CM&E, 2023). However, when combining Lean, digital, artificial intelligence and sustainability, organizations could improve productivity by 30-50%.
How Upskilling Drives Productivity Gains
When your team knows how to improve their own work, results follow—without increasing headcount.
CI supports:
- Shorter onboarding for new hires
- Better documentation
- Less rework and downtime
- Ongoing improvement and innovation
CI builds collective intelligence—employees learn to think systemically, challenge assumptions, and collaborate.
A Deloitte study found teams trained in CI are up to 37% more productive.
Why Employee Engagement Matters
Employee engagement is a productivity multiplier. According to Gallup:
- +14–18% higher productivity
- +23% profitability
- +22% organizational participation
- +10% customer loyalty
CI creates the kind of ownership and participation that fuels these gains.
What Does CI Look Like on the Shop Floor?
CI isn’t abstract—it lives in daily routines:
Practice | Purpose |
Visual boards | Track productivity, scrap, and ideas |
5S | Keep workspaces clean and efficient |
Daily huddles | Solve one issue per day |
Gemba walks | Managers support problem-solving at the source |
Daily Management System | Align work with strategic goals |
📚 Related Reads:
What Results Can You Expect from CI?
Studies show impressive gains when CI is done right:
- 25–30% lower operating costs
- 40–60% faster task completion
- 35% increase in productivity within a year
- 50% fewer defects
- 30% higher customer satisfaction
- 45% fewer customer complaints
- 40% faster time to market
When Is It Time to Automate?
Only once your processes are stable and measurable. Otherwise, you risk:
- Automating waste
- Locking in bad processes
- Wasting capital
As we often say: “Automation helps you produce defects faster.”
Let CI clean the floor before you digitize it.
Where Are Canadian Manufacturers Investing?
Canadian firms are investing in:
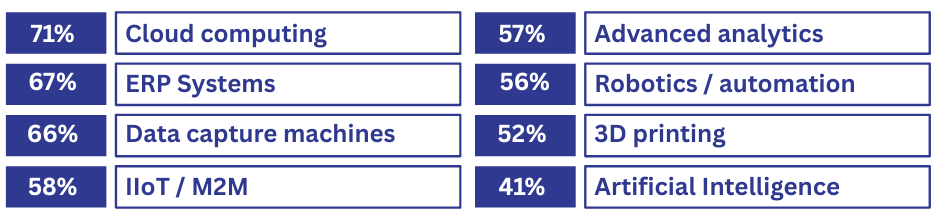
Future Priorities:
- Robotics & automation (66%)
- Shop floor data systems (41%)
- ERP upgrades (41%)
- AI and analytics (34–39%)
(Source: CME Canada 2024)
Take the First Step: Assess Your Operational Maturity
Not sure where to begin?
Try our free Operational Maturity Assessment to:
✅ Identify your current strengths
✅ Uncover hidden productivity gaps
✅ Receive personalized guidance for improvement
Get started with the Teaser Version Here
Ready for more? Get the full version with team-wide insights and improvement priorities.
Final Thoughts: Don’t Automate Chaos—Fix It
Before you expand, digitize, or automate—stabilize your systems.
Continuous improvement creates the clarity, capability, and confidence your team needs to:
- Reduce chaos
- Improve productivity
- Engage meaningfully in change
CI is the launchpad for automation that works—and a stronger workplace culture.
Let’s Start Your Journey to Operational Excellence! Talk to us about how our consulting approach can elevate your processes and empower your teams.
About Veronica B. Marquez, M.Sc., CSSBB
I help growing manufacturing and service organizations scale without chaos—by turning operational challenges into sustainable performance gains. My superpower is making strategy real at every level of the business: connecting people, processes, and purpose to drive productivity, engagement, and resilience. I bring clarity to complexity and help teams execute better, faster, together. Through a proven lens of operational excellence, continuous improvement, and supply chain optimization, I work with leaders to align efforts, simplify execution, and create systems that actually support growth.
Named one of the Top 50 Experts in Operational Excellence by the PEX Network, I bring over 20 years of experience across sectors like manufacturing, distribution, mining, and public services. I teach Lean Six Sigma at the executive education level, lecture on service design in a master’s program, and host a LinkedIn Live series focused on Excellence in Industry 5.0. Ready to explore how operational excellence can transform your business? Reach out https://www.linkedin.com/in/veronicabm/.
📷 Canva