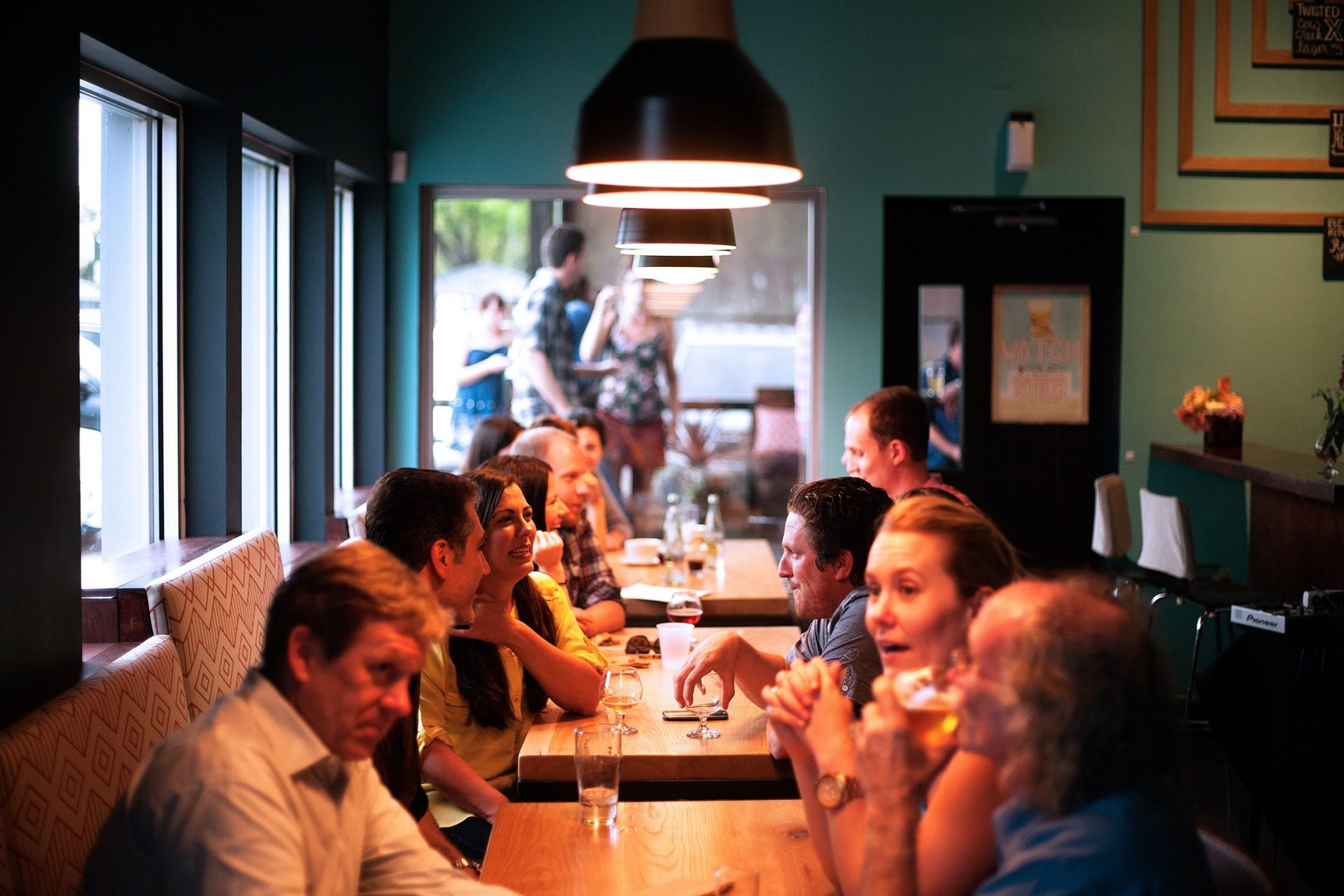
Lean Management is based on the respect for people!
In the last months, several articles about the pandemic claimed that Lean’s just-in-time and cost savings approaches have damaged organizations’ ability to face and adjust to the pandemic. I don’t think I have all the answers, but I do believe that Lean, when understood and applied as a philosophy and culture, would strengthen any organization and help face the unknowns that we have all recently lived.
Some years ago, when I was first introduced to Lean Manufacturing, it was presented as a means for an organization, especially a manufacturing one, to reduce its operations cost. During my employer’s town hall meeting, my colleague who was tasked with implementing Lean principles in our facility, started his address with a speech along the lines of “Today, I’ll speak about…” and presented a branded frozen meal box (I’ll let you guess which one!) I remember thinking how clever and funny he was, and more than 15 years later, that event is still in my memory and has actually inspired this series of articles on Lean Management. This is meant as a way to share how I see Lean Management and how I believe it can contribute to success in organizations of all sizes. In this week’s article, we will look at the foundational elements of Lean, then, on the second one, the balanced approached, and lastly, the Lean Strategy.
Be sure to read the entire series by subscribing to our newsletter.
But first, a clarification is needed. I started this article talking about Lean Manufacturing and then switched to Lean Management, why? Lean has traditionally been linked to manufacturing companies as a way to reduce waste and costs. In the last decades, Lean started to be applied to several other industries, such as healthcare, banking, insurance, construction. I therefore do think that Lean Management is a better way to refer to this philosophy.
Lean Management Elements
Toyota developed its Toyota Production System out of need and a common vision. They trained for years, and still do, to develop their approach, they studied, they learned, the adapted, and they continuously challenge their own status quo. Their success stems from different elements, one of which is that they created a management system that was to be fully integrated within their culture and values.
Culture
Our first element, culture is therefore a strong component of Lean Management in that it sets the tone for our interactions, our communications and our values upon which our decisions are made. Furthermore, having a clear sense of who we are and what we are working to achieve as a team, as members of the same organization, gives us a purpose, which in turn helps us establish a common vision and common objectives for the short and long term, basically our True North.
People
This leads us to our second element, our people. They are the experts at performing their specific tasks and they are the best people to identify what and how we can improve. This is not easy, it requires that we train our employees to identify problems, to work together and to share their ideas within the continuous improvement process. It also requires that we train our supervisors and managers to become coaches and leaders so that they can encourage, train and lead their team members. And that requires that leadership team trust and respect their employees. Why? Because people who feel trusted and respected will speak up, will share their ideas, and will contribute to making the organization a better place. We are then able to stimulate and encourage empowerment and engagement in our team members.
Customers
To create that clear path to what we want to achieve, we search for the voice of the customer. We aim to understand what our customers are looking for, what are their needs, their wants, and how can we reach them. Then, we look at our internal process in relation to the customer’s desires. What are the gaps? What do we need to work on the diminish those gaps and reach our customers’ desires?
Once we have started working on the first elements, we can introduce the fourth one which is the set of standardization approaches that can be applied to help the organization be better structured. Here, we can find the 5S, the visual boards, PDCA and continuous improvement, and process reviews. All these approaches require teamwork, understanding of the common goals, respect of people and of ideas. Without working on the first three ingredients, this final one is almost impossible to mix in.
Is this vision oversimplified? Absolutely!
Why? Because I believe that Lean doesn’t have to be complicated and that it all starts with people. Also, like many recipes that we follow when we cook, sometimes tweaking an ingredient or two, allows us to make the dish even better suited for our family. The same is true with Lean. If we copy what Toyota did, it will not work, because we are not Toyota. Let’s work on understanding what Toyota did and how and the principles, then we can see how we can apply it to our culture, our values, and our people.
CONTACT US TO FIND OUT MORE!
Next week, let’s look at Lean’s balanced approached to improvement. To receive all the articles, subscribe to our newsletter.
_________________________________
About Veronica B. Marquez
I help growing manufacturing and service organizations scale without chaos—by turning operational challenges into sustainable performance gains. My superpower is making strategy real at every level of the business: connecting people, processes, and purpose to drive productivity, engagement, and resilience. I bring clarity to complexity and help teams execute better, faster, together. Through a proven lens of operational excellence, continuous improvement, and supply chain optimization, I work with leaders to align efforts, simplify execution, and create systems that actually support growth.
Named one of the Top 50 Experts in Operational Excellence by the PEX Network, I bring over 20 years of experience across sectors like manufacturing, distribution, mining, and public services. I teach Lean Six Sigma at the executive education level, lecture on service design in a master’s program, and host a LinkedIn Live series focused on Excellence in Industry 5.0. Ready to explore how operational excellence can transform your business? Reach out https://www.linkedin.com/in/veronicabm/.
Photo Credit: pxHere
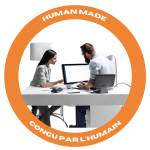
Human made