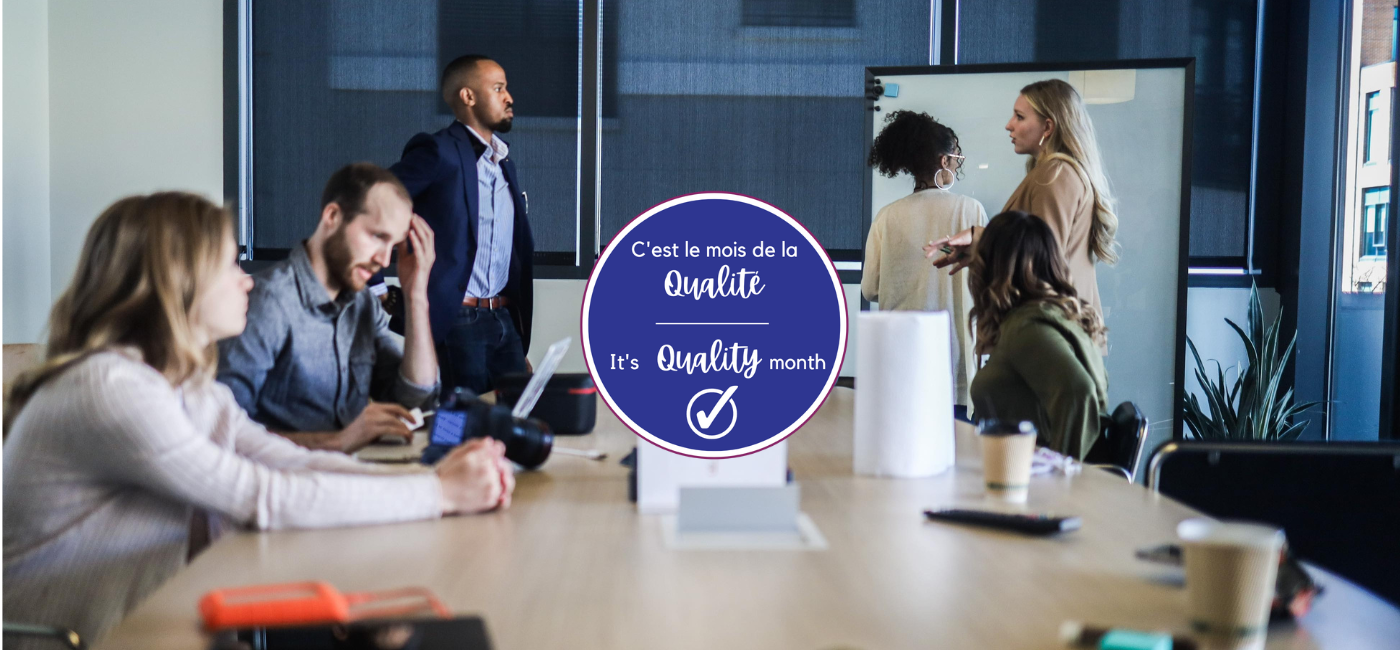
On this Quality Month, we will present a practical tool for brainstorming sessions and for categorization: The fishbone diagram (Also called: cause-and-effect diagram and the Ishikawa diagram).
Are you trying to find a solution to a problem experienced by your team? Have you found the causes of your problem? Well, problem-solving starts with identifying the causes and this is the tool you need!
The cause-and-effect diagram is considered one of the seven quality tools. It can be used to structure a brainstorming session in which we try to understand the many probable causes of a problem. It immediately sorts ideas into useful categories. The most used are the 7Ms, which are Mother Nature, Method, Material, Measurement, Manpower, Management and Machine.
So, when your team’s thinking tends to get bogged down, or when you have difficulty identifying the probable causes of a problem, it is time to use the cause-and-effect diagram!
How do you use the Fishbone Diagram?
- On a whiteboard and with some markers, draw a horizontal arrow across the board.
- At the end of the arrow, indicate the problem for which you are looking for causes.
- Write down the categories (the 7Ms) as branches from the main arrow.
- Then look at the main categories and add the reasons on each branch. There may be causes that apply to several categories. Here, we are looking for the maximum number of ideas without assessing their merit.
For each branch, ask yourself:
- Why is this happening?
- What is causing the problem?
- What internal and external factors have an impact?
Once the diagram is complete, the next question is what to work on. This part of the exercise often requires additional data, for example, reasons for defects, reasons for delays, etc. The goal is then to give weight to each cause mentioned in order to determine which are the most important ones that we can change and work on.
The fishbone diagram is an indispensable tool for the ideation of the causes of our problems and together with data and observations, it will allow us to address the right causes to solve the issues.
CONTACT US TO FIND OUT MORE!
____________________________________
About Veronica B. Marquez
I help growing manufacturing and service organizations scale without chaos—by turning operational challenges into sustainable performance gains. My superpower is making strategy real at every level of the business: connecting people, processes, and purpose to drive productivity, engagement, and resilience. I bring clarity to complexity and help teams execute better, faster, together. Through a proven lens of operational excellence, continuous improvement, and supply chain optimization, I work with leaders to align efforts, simplify execution, and create systems that actually support growth.
Named one of the Top 50 Experts in Operational Excellence by the PEX Network, I bring over 20 years of experience across sectors like manufacturing, distribution, mining, and public services. I teach Lean Six Sigma at the executive education level, lecture on service design in a master’s program, and host a LinkedIn Live series focused on Excellence in Industry 5.0. Ready to explore how operational excellence can transform your business? Reach out https://www.linkedin.com/in/veronicabm/.
Source: : https://asq.org/quality-resources/fishbone#Example
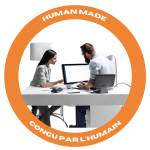
Human made