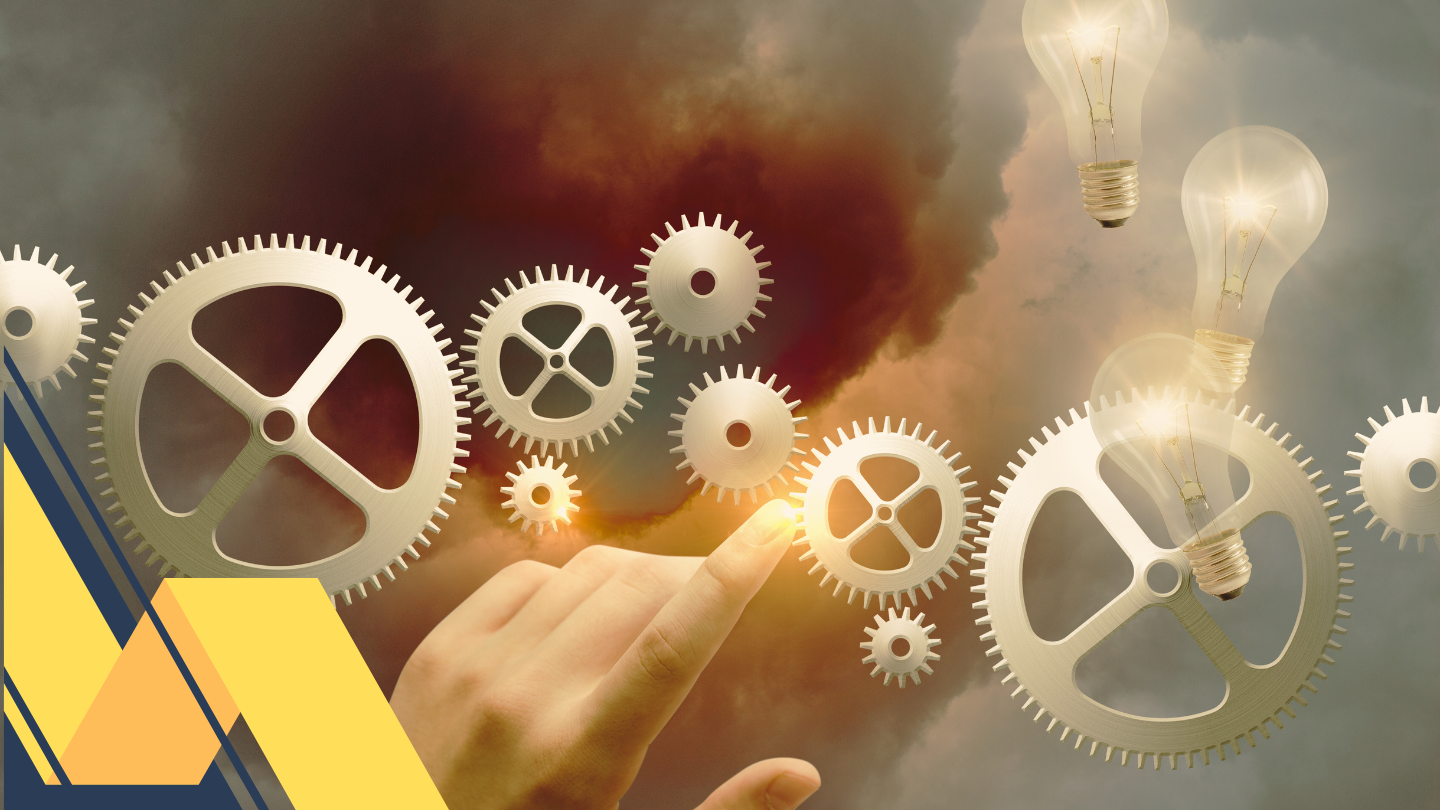
In today’s competitive business landscape, organizations are constantly seeking ways to streamline operations, reduce waste, and improve productivity and overall efficiency. Enter Lean Six Sigma, a powerful methodology that has revolutionized process improvement across industries. At the heart of this transformative approach lies a structured hierarchy of expertise, with the Yellow Belt serving as the crucial first step on the path to process mastery. Let’s delve into the world of Lean Six Sigma Yellow Belt training, exploring its significance, benefits, and the essential role it plays in empowering team members to drive meaningful change within their organizations.
The Evolution of Process Improvement: Understanding Lean Six Sigma
Before we dive into the specifics of Yellow Belt training, it’s essential to understand the broader context of Lean Six Sigma. This methodology represents the culmination of decades of process improvement thinking, combining the waste-reduction focus of Lean manufacturing with the defect-elimination principles of Six Sigma. Originating in the manufacturing sector, Lean Six Sigma has since found applications across diverse industries, from healthcare to finance, proving its versatility and effectiveness in tackling a wide array of operational challenges.
At its core, Lean Six Sigma is about creating value for customers by optimizing processes, reducing variability, and eliminating defects. It employs a data-driven approach, utilizing statistical tools and a structured problem-solving methodology known as DMAIC (Define, Measure, Analyze, Improve, Control). This systematic framework allows organizations to identify root causes of inefficiencies, implement targeted solutions, and sustain improvements over time.
The Yellow Belt: Gateway to Process Improvement Excellence
Within the Lean Six Sigma framework, practitioners are classified into various levels of expertise, denoted by coloured belts. The Yellow Belt is the entry-level certification and a foundational step for individuals starting their process improvement journey. Importantly, the Yellow Belt plays a crucial role in spreading Lean Six Sigma principles throughout an organization. Thus, it creates a common language and mindset that fosters a culture of continuous improvement.
Yellow Belt holders are typically team members participating in process improvement projects led by more experienced Green or Black Belts. They have a basic understanding of Lean Six Sigma concepts and tools. Consequently, they can contribute effectively to improvement initiatives while continuing their primary job functions. This dual role makes Yellow Belts invaluable assets. They can identify improvement opportunities in their daily operations and collaborate with higher-level practitioners to implement solutions.
Our approach to Yellow Belt training is distinctive. We believe in learning by doing. Therefore, our certification path involves managing a continuous improvement project. This hands-on experience allows learners to apply Lean Six Sigma principles in real time. They gain practical skills and insights. Transitioning from theory to practice is seamless. Ultimately, this method ensures that knowledge is not just acquired but effectively implemented.
The Multifaceted Benefits of Yellow Belt Training
Investing in Yellow Belt training yields a multitude of benefits, both for individual team members and the organization as a whole. Let’s explore some of the key advantages:
1. Enhanced Problem-Solving Skills
Yellow Belt training equips participants with a structured approach to problem-solving, teaching them to analyze processes critically and identify areas for improvement. This analytical mindset extends beyond specific projects, enhancing overall decision-making capabilities in various aspects of their work.
2. Improved Communication and Collaboration
By introducing a common language and set of tools, Yellow Belt training facilitates better communication among team members and across departments. This shared understanding promotes more effective collaboration on improvement initiatives and helps break down silos within the organization.
3. Increased Employee Engagement and Empowerment
Yellow Belt certification gives team members a sense of ownership in the improvement process, empowering them to contribute ideas and take an active role in enhancing their work environment. This increased engagement often leads to higher job satisfaction and improved morale.
4. Employee Development Opportunities
As organizations increasingly recognize the value of Lean Six Sigma skills, Yellow Belt training provides employees with valuable skills and knowledge that enhance their personal and professional development. This certification fosters a culture of continuous improvement and empowers individuals to take initiative in their roles. As employees grow and develop, they become more capable, motivated, and engaged, driving overall organizational success. The organization benefits through increased productivity, innovation, and a more skilled workforce, all of which contribute to achieving strategic goals and maintaining a competitive edge in the market.
5. Tangible Business Impact
With a team of Yellow Belt-certified employees, organizations can tackle a wider range of improvement projects simultaneously, leading to cumulative gains in productivity, efficiency, quality, employee engagement, and customer satisfaction.
Core Concepts Covered in Yellow Belt Training
Yellow Belt training provides a comprehensive introduction to Lean Six Sigma principles and tools. Our training is based on our more than 20 years of experience leading process improvements initiatives. Every training is tailored to the need of our client and these are the topics elements covered in our training:
1. Introduction to Quality
Trainees learn the history, philosophies, and evolution of the quality movements leading into continuous improvement and Lean Six Sigma.
2. Continuous Improvement: Team Effort
An overview of the importance of the team in working on continuous improvement projects. We define and review each role in a project to align the efforts and reach the objectives
3. Introduction to Lean Six Sigma
Trainees learn the history, philosophy, and basic principles of Lean Six Sigma, including the concepts of value, waste, and continuous improvement.
4. The DMAIC Methodology
An overview of the Define, Measure, Analyze, Improve, and Control phases, providing a structured approach to problem-solving and process improvement.
5. Project Management
Trainees learn the intricacies of managing a project and the stages of teams, so that they can better lead the initiative and reach the desired results.
6. Coaching through the first project
Learning to drive is not just about following the training, it requires practice. The same is true of Yellow Belt training. Therefore, our training methodology includes coaching during the first project to ensure that trainees fully understand the approach and the tools and can effectively move their project toward results.
Our Training Approach
The training is rigorous and detailed. We support our clients in the selection of the team members as well as the projects that will be launched from this training. After the training, trainees will have to confirm understanding through an exam. Once they successfully complete their project and demonstrate an effective application and results, they will receive the Lean Six Sigma Yellow Belt Certification.
Empowering Team Success through Yellow Belt Training
The impact of Yellow Belt training extends beyond individual skill development. It fosters a culture of continuous improvement within organizations. By equipping team members with Lean Six Sigma principles, Yellow Belt training creates a workforce that identifies waste, inefficiencies, and opportunities for enhancement in daily operations.
This awareness, combined with problem-solving tools from training, enables Yellow Belts to contribute to improvement initiatives. They gather and analyze data, participate in brainstorming sessions, and help implement and sustain improvements. Furthermore, Yellow Belts bridge improvement teams and their departments, ensuring solutions are tailored to specific needs and constraints.
Moreover, Yellow Belt-certified team members create a multiplier effect within the organization. As more employees learn Lean Six Sigma principles, the potential for identifying and executing improvement projects increases. This knowledge base allows organizations to tackle various challenges, from small process tweaks to comprehensive transformations.
Additionally, Yellow Belt training demystifies the process improvement journey. It makes the concepts more accessible and less intimidating for new team members. This inclusivity is crucial for building a sustainable culture of continuous improvement, where every employee feels empowered to contribute ideas and drive positive change.
Embarking on Your Lean Six Sigma Journey: The Call to Action
Lean Six Sigma Yellow Belt training represents a pivotal first step in mastering the art and science of process improvement. It offers a unique blend of personal skill development and organizational impact, making it an invaluable investment for both individuals and companies alike.
For Organizations
Investing in Yellow Belt training for employees is a strategic move that can yield significant returns. By creating a foundation of Lean Six Sigma knowledge across the workforce, companies can accelerate their improvement initiatives, foster a culture of innovation, and build a competitive edge in today’s fast-paced business environment.
For Team Members
For team members looking to enhance their problem-solving capabilities, contribute more effectively to their organizations, and potentially unlock new career opportunities, Yellow Belt certification provides an excellent starting point. The skills and knowledge gained through this training are immediately applicable, offering tangible benefits from day one.
As you consider the next steps in your organizational improvement strategy, we encourage you to explore our Lean Six Sigma Yellow Belt training. Taking this first step on the Lean Six Sigma journey can open a world of possibilities for business success.
Remember, the path to process mastery begins with a single step. By embracing the Yellow Belt training, you’re not just learning a set of tools and techniques; you’re adopting a mindset of continuous improvement that can transform the way your organization approaches challenges and opportunities. Take that step today! Join the ranks of organizations who are driving innovation and excellence across industries through the power of Lean Six Sigma.
📷 Canva