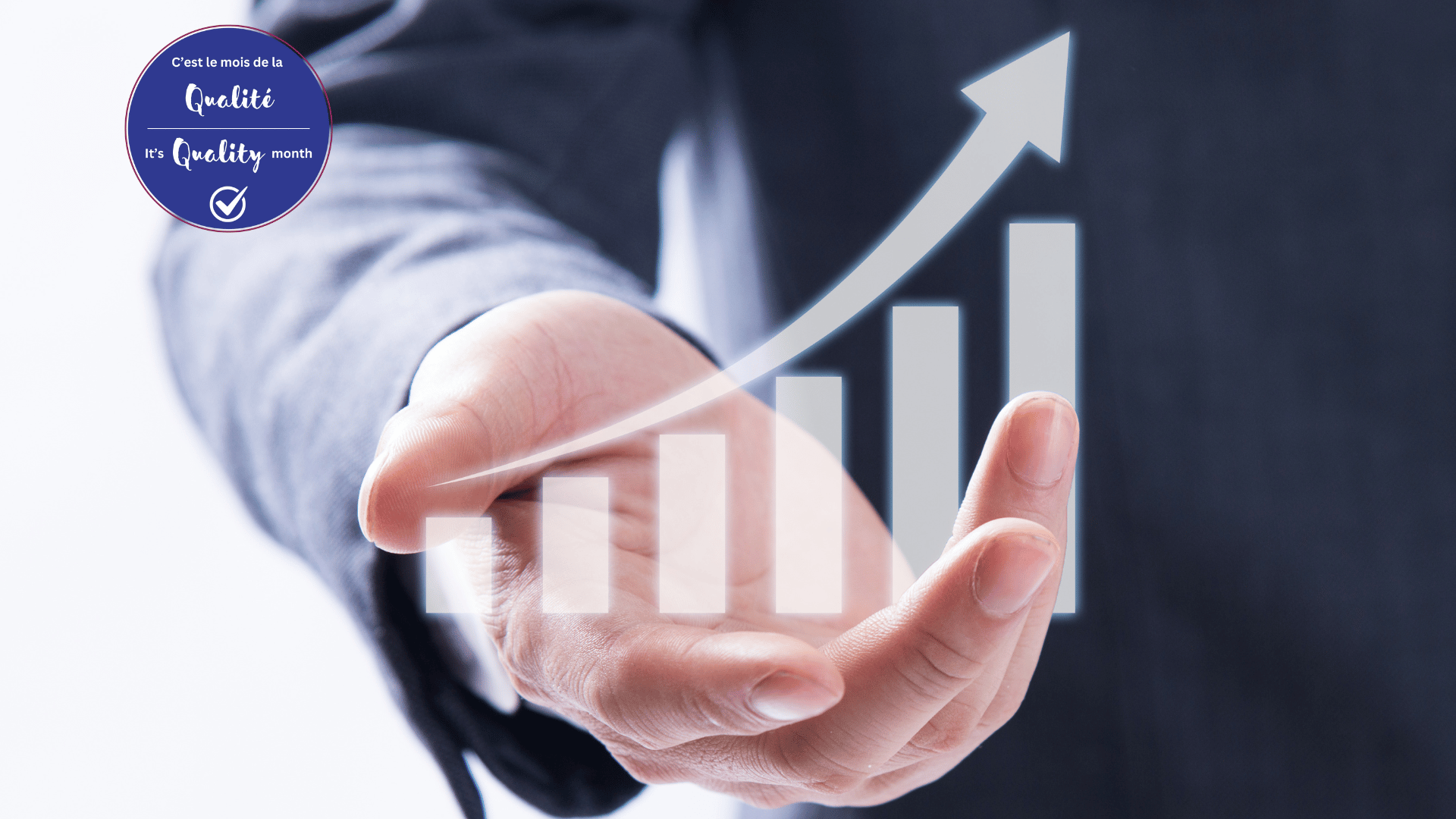
Few tools are as powerful as control charts in the world of quality and process management. Yet, despite their proven effectiveness, many operations managers and quality control specialists are not fully harnessing their potential. If you’re looking to enhance efficiency, reduce waste, or simply understand your processes better, control charts might be the missing piece in your puzzle.
This blog post will walk you through the essentials of control charts, their benefits, and how you can implement them effectively in your operations.
Understanding Control Charts
Control charts are graphical tools used to monitor the stability of processes over time. Developed by Walter Shewhart in the 1920s, these charts are pivotal in spotting variations within processes. They display data points over time and highlight any variations that fall outside of the set control limits. This can clue managers into potential issues and areas for improvement.
The control limits on these charts are determined mathematically. Specifically, they are set at three standard deviations above and below the average. This statistical approach ensures that the process is monitored with precision. Such accuracy allows managers to distinguish between normal variations and significant, potentially problematic deviations.
This concept has been championed by many experts, including Edward Deming, who emphasized their role in quality control. Deming noted, “In God we trust; all others bring data,” underscoring the importance of data-driven decisions in operational management.
Why Use Control Charts?
Using control charts is like having a continuous feedback loop for your processes. They provide a visual representation of how a process is performing, making it easier to spot trends and anomalies. This visual clarity can help managers take preemptive actions before minor issues become major problems, ensuring a smoother operational flow.
Control charts are invaluable in ensuring consistent product quality. By consistently monitoring a process, you can ensure that it remains within the desired limits, reducing the risk of defects. These charts along with the minor nonconformities recorded are a powerhouse of prevention. This consistency not only boosts product quality but also improves customer satisfaction—a key goal for any business.
Furthermore, control charts can save significant time and resources. By quickly identifying areas of concern, they can reduce the need for extensive investigations and troubleshooting. This efficiency can translate to cost savings and a more streamlined operation.
How to Use and Interpret Control Charts
Implementing control charts is relatively straightforward, but interpreting them correctly requires a solid understanding of their components. At their core, they consist of a central line (representing the average), upper and lower control limits, and plotted data points.
To use a control chart effectively, start by collecting data over a period. This data could relate to product dimensions, weights, or any quantifiable metric relevant to your process. Once collected, plot these data points on the chart.
The key to interpreting control charts lies in understanding what the data points represent. If data points consistently fall within the control limits, it suggests that the process is stable. However, intervention is needed if points start to drift towards the limits or fall outside them.
It’s important to remember that not all variations are signs of problems. Control charts help differentiate between common cause variations (natural fluctuations) and special cause variations (indicative of problems). By focusing only on the latter, managers can ensure that their interventions are targeted and effective.
Benefits of Tracking Control Charts
The benefits of using control charts in your operations are manifold.
- they offer a clear visual representation of a process’s stability, making it easier to communicate performance to stakeholders. This transparency fosters collaboration and ensures that everyone is on the same page regarding process quality.
- control charts can significantly enhance process efficiency. By identifying and addressing variations early, businesses can reduce waste, save time, and optimize resources. This proactive approach can lead to significant cost savings and improved profitability.
- tracking control charts strengthens quality control. With a consistent monitoring approach, businesses can continuously improve their processes, leading to higher product quality and increased customer satisfaction. This continuous improvement mindset is essential in today’s competitive market.
Getting Started
For those looking to implement control charts in their operations, the process begins with data collection. Identify the key metrics that matter most to your business and that are aligned with the strategic goals and start gathering data over a set period. This foundational step is crucial, as the accuracy of your control charts depends on the quality of the data collected.
Once you have sufficient data, plot it on a control chart and establish your control limits. This will lay the groundwork for effective monitoring. Remember, the goal is not just to collect data but to understand and act on it.
Lastly, integrate control charts into your regular operational daily and weekly reviews. By making them a part of your routine, you can ensure that they remain a valuable leading indicator in your quality control arsenal. This integration will empower your team to take data-driven decisions, enhancing overall operational efficiency.
Conclusion
Control charts are an indispensable tool for any quality or operations manager. By offering a clear visual representation of process stability, they empower businesses to make informed, data-driven decisions. From enhancing product quality to optimizing operations, their benefits are vast and impactful.
For those new to control charts, the key is to start simple. Begin by identifying the metrics that matter most to your operations, collect data, and plot them on a chart. With time and practice, you’ll gain a deeper understanding of your processes and the confidence to act on your insights.
Remember, in the words of Edward Deming,
Control charts provide the data you need to transform opinions into actionable insights, driving success in today’s competitive market.
If you’re ready to take the next step in optimizing your operations with control charts, we are here to guide you through every stage of implementation, ensuring that you harness the full potential of this powerful tool. Reach out today to begin your journey toward enhanced efficiency and quality.
To learn more about Control charts visit https://deming.org/a-beginners-guide-to-control-charts/
____________________________________
About Veronica B. Marquez
I help growing manufacturing and service organizations scale without chaos—by turning operational challenges into sustainable performance gains. My superpower is making strategy real at every level of the business: connecting people, processes, and purpose to drive productivity, engagement, and resilience. I bring clarity to complexity and help teams execute better, faster, together. Through a proven lens of operational excellence, continuous improvement, and supply chain optimization, I work with leaders to align efforts, simplify execution, and create systems that actually support growth.
Named one of the Top 50 Experts in Operational Excellence by the PEX Network, I bring over 20 years of experience across sectors like manufacturing, distribution, mining, and public services. I teach Lean Six Sigma at the executive education level, lecture on service design in a master’s program, and host a LinkedIn Live series focused on Excellence in Industry 5.0. Ready to explore how operational excellence can transform your business? Reach out https://www.linkedin.com/in/veronicabm/.
📷 Canva
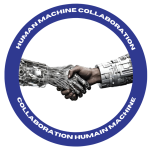