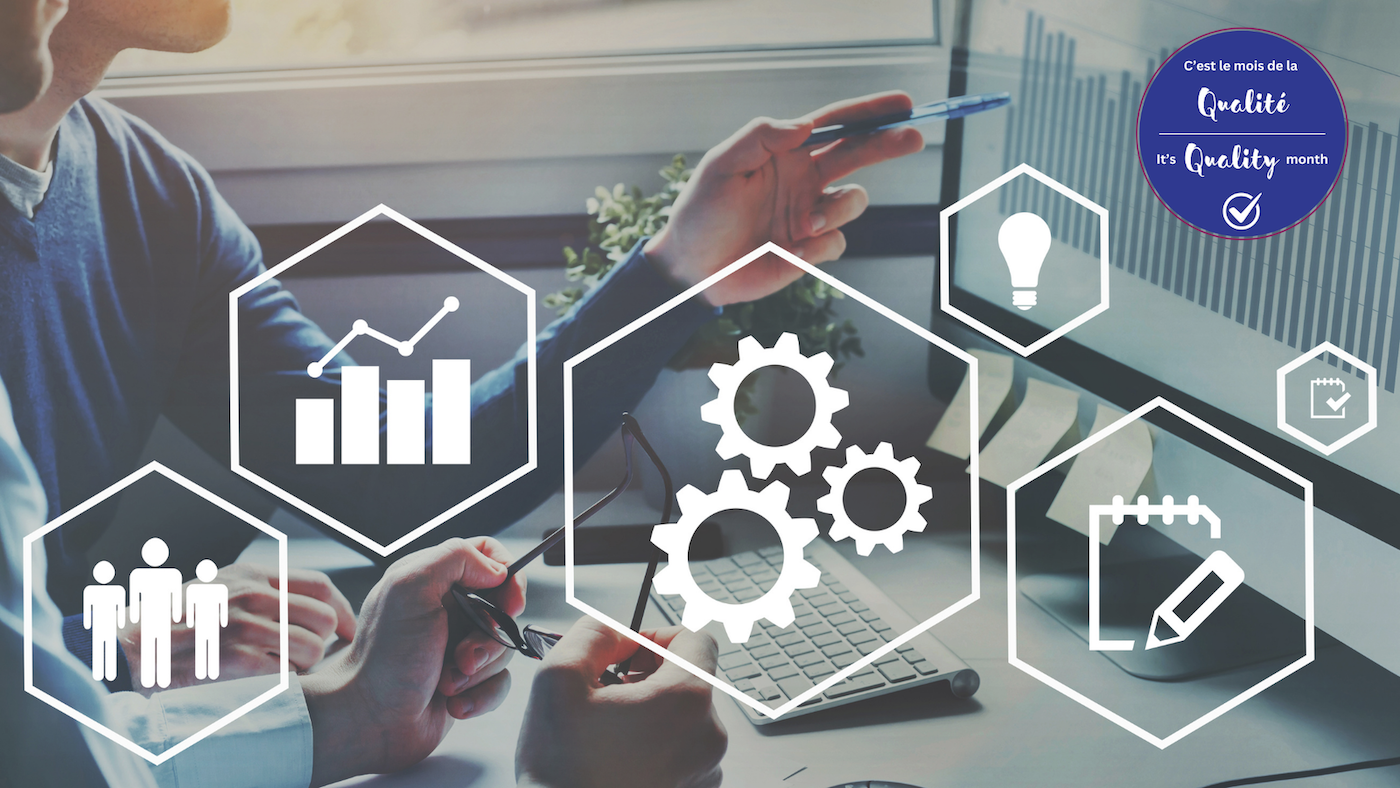
Working to improve a process? Then an SIPOC is one of the key tools to use to better understand the scope of your task.
Understanding the Tool
An SIPOC is a visual representation that shows the process on which the team is focusing and the elements that come before it and after it. We use the SIPOC to better understand what is impacting and driving our process. This means that we look at the suppliers and what they contribute to the process. Then, we also look at the outputs of the process and who the clients are.
This approach helps us to better understand the scope of the project, where the process begins and ends for the continuous improvement team, as well as understand how it fits within a larger business process.
The Five Elements of SIPOC
When documenting an SIPOC, we look at these five key components: Supplier, Input, Process, Output, and Customer.
For example, if we are working on a process to improve the purchasing of items for production, we would have the following information:
Through the diagram, we can see the different elements and people that have an impact on the process and that can be impacted by it as well. The SIPOC lets us see and determine where our process begins and ends so that we can clearly establish the elements that will be in and out of the scope of the project.
The Benefits of SIPOC
In a business, no process is isolated. All the different key players and steps to deliver the goods or services promised are interconnected and interwoven. Hence, understanding how processes and people are linked is critical in making sure that CI teams address the right issues without causing further issues in another area.
An SIPOC helps us do just that. By looking at who contributes the inputs for the process, we can understand the work and information flows that impact our process and stakeholders. In the same manner, we can understand the outputs generated by our process and who the clients are so that we can see how we impact further processes down the line.
Sometimes in an SIPOC, we will see disconnected elements or some that don’t show a correlation with other parts of the diagram. These isolated elements that show up on the SIPOC become new opportunities for improvement. Through this systemic visibility, we can make sure that nothing is treated in isolation and that we solve the issues, we don’t moved them to another team.
Implementing SIPOC
To build the SIPOC, gather the people who are experts of the overall process, i.e., the people who work in it every day! This session will be most effective when facilitated by a person who is not part of the process. The facilitator’s role will ensure that everyone stays on task and is focused on the objective. Ensure that everyone understands the objectives of the meeting:
- identify what part of the process they will focus on during the CI initiative (the scope of the project)
- understanding the upstream and downstream elements of the process.
In our example above, we would invite to the table,
- For the supplier side:
- Representatives of the clients and end users if they were not able to attend themselves.
- Supply chain planners.
- Production supervisors.
- For the client side:
- Suppliers
- Carriers
- Warehouse supervisors
- Distribution supervisors
- Representatives of the clients and end users if they were not able to attend themselves.
Together, this group will be able to explain what they provide in terms of input into the process and what they expect as output of the process.
SIPOC and Lean Six Sigma
When we work in a Six Sigma DMAIC process improvement project, we use the SIPOC in the Define phase. It helps to better understand the problem at hand, how it fits within the overall organization as well as who is impacted by it.
Lean Six Sigma aims at improving the organization through process improvement. But it can be easy to focus only on a small part of the process without understanding how it affects the overall process. We want to solve problems, not move them upstream or downstream and the SIPOC tool helps us do just that. Therefore, the SIPOC offers us a systemic view of the process. It shows how it fits within the overall business processes and ensures that the improvement is sound and company-wide.
Overcoming Challenges with SIPOC
When building a SIPOC, it can be tempting to include a lot of elements on the diagram. However, short and easy goes a long way! The point is not to document each step of the process on the SIPOC. But rather show a high-level view of what is in scope. The detailed process map will be later in the Measure phase.
Leveraging for Supply Chain Optimization
A supply chain is a series of activities required to bring a product or service to its final consumer, see our article “What’s a Supply Chain” for more details. Because of its many parts, people, and processes involved, a supply chain continuous improvement effort is managing several upstream and downstream processes. Using the SIPOC will not only help in making sure that team members understand the impact of the process, but it can also generate insights that can reduce lead times and improve throughput.
In conclusion, the SIPOC is a quality tool that illustrates the upstream and downstream of a process, the people involved, and the key inputs and outputs of said the process. Running an SIPOC exercise allows to align the CI team members on the scope of the project, identify opportunities for improvement, and streamline the process to better serve the customers.
Ready to Streamline Your Processes? Book your free consultation and get started today!
____________________________________
About Veronica B. Marquez
I help growing manufacturing and service organizations scale without chaos—by turning operational challenges into sustainable performance gains. My superpower is making strategy real at every level of the business: connecting people, processes, and purpose to drive productivity, engagement, and resilience. I bring clarity to complexity and help teams execute better, faster, together. Through a proven lens of operational excellence, continuous improvement, and supply chain optimization, I work with leaders to align efforts, simplify execution, and create systems that actually support growth.
Named one of the Top 50 Experts in Operational Excellence by the PEX Network, I bring over 20 years of experience across sectors like manufacturing, distribution, mining, and public services. I teach Lean Six Sigma at the executive education level, lecture on service design in a master’s program, and host a LinkedIn Live series focused on Excellence in Industry 5.0. Ready to explore how operational excellence can transform your business? Reach out https://www.linkedin.com/in/veronicabm/.
Sources:
https://asq.org/quality-resources/sipoc
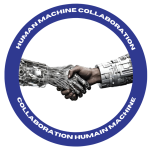